Acetone-to-Cumene (ATC) Technology
Badger Acetone-to-Cumene (ATC) technology offers a low capital investment with simple integration into existing cumene plants. The design of the unit allows for easy and safe unit operation with a high reliability and high on-stream time.

For cumene producers seeking an alternative feedstock to propylene, looking to capitalize on the phenol-acetone imbalance that may exist in the market, or looking to maximize profits through arbitrage of the fluctuations in propylene, IPA, and acetone pricing, Badger’s ATC technology offers the perfect solution at a low capital investment.
Badger ATC technology offers flexibility and can be applied to produce cumene from 100% acetone feed or can be integrated in standard propylene-based cumene plants using partial recycle of acetone from an associated phenol plant.
Resources
The Acetone-to-Cumene (ATC) Process
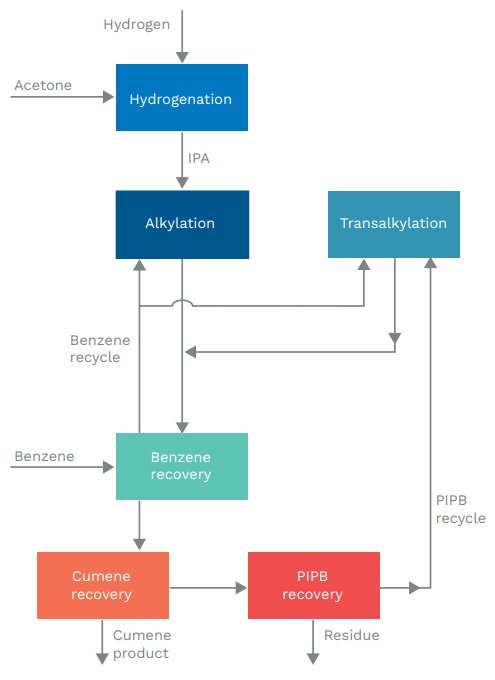
Hydrogenation
A nickel catalyzed hydrogenation system converts acetone and hydrogen to isopropanol (IPA).
Alkylation
An alkylation reactor system converts benzene and IPA to cumene in the liquid phase. A small fraction of the cumene is further alkylated to PIPB which will be recovered in distillation and converted to cumene in the transalkylation reactor.
Transalkylation
A single bed transalkylation reactor converts the small amount of PIPB formed in the alkylator to additional cumene by reaction with benzene in the liquid phase.
Purification
A simple energy efficient distillation train is used to return excess unreacted benzene to the alkylation and transalkylation reactors, recover cumene product and recycle PIPB to transalkylation.
Low Operating Cost
- Ultra-high (nearly stoichiometric) yields minimize raw material consumptions
- The alkylation catalyst used can tolerate high water concentration, requiring less circulation
Low Capital Investment
- Low benzene and isopropanol and Bz/PIPB ratios results in smaller reaction and distillation equipment
- Small catalyst volumes
- Low temperature, pressure, and non-corrosive conditions allows carbon steel construction
Contact our Experts
Kenneth Potochnik
- kenneth.potochnik@ten.com
- Tel: +1 617-748-7272